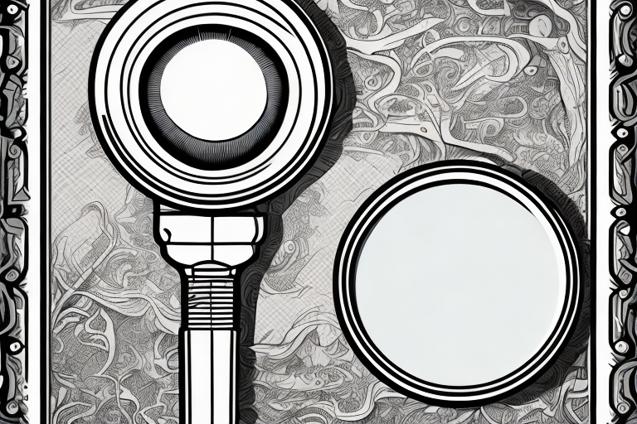
Having access to a reliable source of fresh water is essential for long-term sailing adventures. This comprehensive guide provides troubleshooting tips and solutions for common watermaker issues, along with preventative maintenance advice to keep your watermaker running smoothly.
Troubleshooting Common Watermaker Issues
Welcome to our unique and adventurous website, dedicated to those who are leaving the rat race behind, purchasing a boat, and setting sail to explore the world with their families. In this article, we will discuss common watermaker issues and how to troubleshoot them. Watermakers are essential for long-term sailing adventures, as they provide a reliable source of fresh water by converting seawater into potable water through a process called desalination. However, like any piece of equipment, watermakers can experience issues that may affect their performance or cause them to stop working altogether.
In this comprehensive guide, we will cover the following topics:
- Understanding the basics of watermakers and desalination
- Common watermaker issues and their causes
- Troubleshooting tips and solutions for each issue
- Preventative maintenance to keep your watermaker running smoothly
Understanding the Basics of Watermakers and Desalination
Before diving into troubleshooting, it’s essential to understand how watermakers work and the process of desalination. Watermakers use a process called reverse osmosis to remove salt and other impurities from seawater, producing fresh, potable water. This process involves forcing seawater through a semi-permeable membrane, which allows water molecules to pass through while trapping larger salt ions and other impurities.
There are several components in a watermaker system, including:
- High-pressure pump: Increases the pressure of the seawater to force it through the membrane
- Reverse osmosis membrane: The semi-permeable membrane that separates fresh water from saltwater
- Prefilters: Remove larger particles and debris from the seawater before it reaches the high-pressure pump and membrane
- Postfilters: Further purify the fresh water after it has passed through the membrane
- Flow meters and gauges: Monitor the system’s performance and water quality
Now that we have a basic understanding of watermakers and desalination let’s discuss some common issues and how to troubleshoot them.
Common Watermaker Issues and Their Causes
There are several common issues that can affect the performance of your watermaker. These include:
- Low or no water production
- Poor water quality
- Leaks
- High-pressure pump issues
- Membrane fouling or damage
1. Low or No Water Production
If your watermaker is producing little to no water, there could be several causes, including:
- Insufficient water flow to the high-pressure pump
- Clogged pre-filters
- Air in the system
- Damaged or worn high-pressure pump components
- Fouled or damaged reverse osmosis membrane
2. Poor Water Quality
If the water produced by your watermaker tastes salty or has an unpleasant odor, it could be due to:
- A damaged or fouled reverse osmosis membrane
- Insufficient pressure in the system
- Clogged post-filters
3. Leaks
Leaks in your watermaker system can occur in various locations, including:
- High-pressure pump seals
- Membrane housing
- Fittings and connections
4. High-Pressure Pump Issues
Problems with the high-pressure pump can result in low water production or poor water quality. Common issues include:
- Worn or damaged pump components
- Insufficient water flow to the pump
- Air in the system
5. Membrane Fouling or Damage
A fouled or damaged reverse osmosis membrane can cause low water production, poor water quality, or both. Common causes of membrane fouling include:
- Biofouling: The growth of microorganisms on the membrane surface
- Scaling: The buildup of mineral deposits on the membrane surface
- Particulate fouling: The accumulation of particles and debris on the membrane surface
Troubleshooting Tips and Solutions for Each Issue
Now that we’ve identified some common watermaker issues and their causes, let’s discuss how to troubleshoot and resolve them.
1. Low or No Water Production
- Insufficient water flow to the high-pressure pump: Check the seawater intake for blockages or debris and ensure the intake strainer is clean. Also, verify that the pre-filters are not clogged and are allowing adequate water flow.
- Clogged pre-filters: Inspect and clean or replace the pre-filters as needed.
- Air in the system: Bleed the system to remove any trapped air, following the manufacturer’s instructions.
- Damaged or worn high-pressure pump components: Inspect the pump for signs of wear or damage and replace any necessary components.
- Fouled or damaged reverse osmosis membrane: Clean or replace the membrane as needed (see the “Membrane Fouling or Damage” section below for more information).
2. Poor Water Quality
- Damaged or fouled reverse osmosis membrane: Clean or replace the membrane as needed.
- Insufficient pressure in the system: Check the high-pressure pump and system pressure to ensure it is within the manufacturer’s recommended range. Adjust the pressure as needed.
- Clogged post-filters: Inspect and clean or replace the post-filters as needed.
3. Leaks
- High-pressure pump seals: Inspect the pump seals for signs of wear or damage and replace them as needed.
- Membrane housing: Check the membrane housing for cracks or damage and replace it if necessary.
- Fittings and connections: Inspect all fittings and connections for leaks and tighten or replace them as needed.
4. High-Pressure Pump Issues
- Worn or damaged pump components: Inspect the pump for signs of wear or damage and replace any necessary components.
- Insufficient water flow to the pump: Check the seawater intake for blockages or debris and ensure the intake strainer is clean. Also, verify that the pre-filters are not clogged and are allowing adequate water flow.
- Air in the system: Bleed the system to remove any trapped air, following the manufacturer’s instructions.
5. Membrane Fouling or Damage
- Biofouling: Clean the membrane using a biocide solution, following the manufacturer’s instructions.
- Scaling: Clean the membrane using a descaling solution, following the manufacturer’s instructions.
- Particulate fouling: Flush the membrane with fresh water to remove any accumulated particles and debris.
- Damaged membrane: If the membrane is damaged, it will need to be replaced.
Preventative Maintenance to Keep Your Watermaker Running Smoothly
Regular maintenance is crucial to keep your watermaker running smoothly and prevent issues from arising. Some essential preventative maintenance tasks include:
- Regularly inspecting and cleaning or replacing pre-filters and post-filters
- Flushing the system with fresh water after each use to prevent fouling and scaling
- Periodically checking the system pressure and adjusting as needed
- Inspecting the high-pressure pump and other components for signs of wear or damage
- Regularly checking for leaks and addressing them promptly
- Following the manufacturer’s recommendations for membrane cleaning and replacement
By staying vigilant with preventative maintenance and addressing any issues promptly, you can ensure that your watermaker continues to provide fresh, clean water for you and your family throughout your sailing adventures.